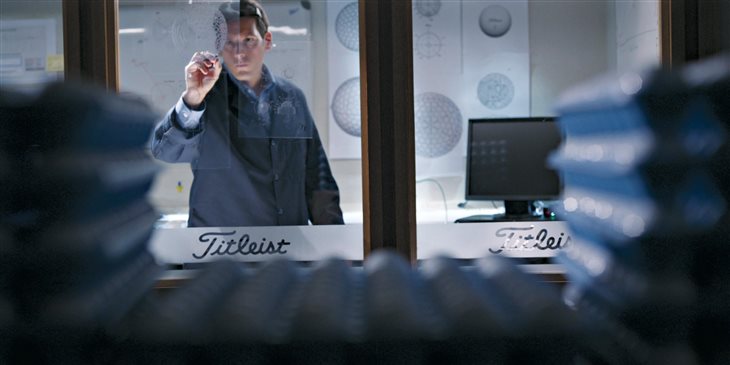
Paint spraying onto twirling golf balls. The zap heard during corona discharge. The sight of a golf ball earning the Titleist script.
These are just some of the sights and sounds experienced in our golf ball plants, manufacturing the #1 ball in golf.
We went behind the curtain of Ball Plant 3 in New Bedford, Mass., to see some of the steps that go into making a Pro V1 golf ball. Let's take a closer look:
Once the core materials are molded, Pro V1 cores undergo Titleist's corona discharge process. This process ensures that the Urethane Elastomer™ cover adheres properly to the core.
Our Urethane Elastomer™ formulation and the process to make it is what sets Titleist apart from the rest. Our cover system technology enables us to cast extremely thin covers, control the uniformity, and tailor it to your game.
Thanks to our paint system developed by Golf Ball R&D, Pro V1 and Pro V1x stay whiter and brighter longer throughout the course of play. The cover and paint system also contributes to an aerodynamically more consistent golf ball.
The Titleist Operations team has grown to more than 1,100 associates with an average tenure of 20 years and over 20,000 years of collective experience. These associates assure that every golf ball performs consistently for every golfer, every round and on every type of shot.
Throughout this rigorous process, the Titleist golf ball has earned its script. Our commitment to continuous improvement and performance and quality excellence are core values of the Titleist tradition, which the golfer gets to experience every time he or she tees up the #1 ball in golf.